All Articles
Analytical Chemistry
Maintenance
Anger Management & Related Issues
Marketing
Antitrust
Medical - Medicine
Appraisal & Valuation
Meditation
Architecture
Physician Assistants
Biomechanics
Pollution - Air Quality Control
Blockchain Information
Pools and Spas (Recreational)
Business Consulting
Postal Services
Casinos - Gambling - Gaming
Professional Malpractice
Computer Forensics
Psychology
Credit Damage
Public Speaking
Elevators - Escalator - Automatic Doors
Real Estate
Emergency Medicine
Refrigeration - Cooling Systems
Engineering
Search Engine Optimization (SEO)
Exercise Equipment
Security
Expert Witnessing
Social Issues
Failure Analysis
Speech-Language Pathology
Fall Protection Solutions / Confined Spaces Safety
Technology
Family Issues
Telecommunication
Food & Beverage
Trial Presentations - Demonstrative Evidence
Hotels & Hospitality
Trusts & Estates
Industrial Equipment
Underwriting
Islamic & Sharia Law
Vocational Rehabilitation And Counseling
Land Mapping - Surveying - Zoning
Wilderness Emergency Medicine
Legal Issues
Yoga
More...
Business consultants
Keywords
Category
Name
Company
Address
State
*Enter State Names or Abbreviations. Use space to separate multiple states e.g. CA Washington NY
Country
All Articles
Accident Prevention & Safety
Meteorology
Advertising
Neuropsychology
All-Terrain Vehicles (ATV / UTV)
Optometry
Animals
Orthotics and Prosthetics
Arms - Guns - Weapons
Pain Management
Banking
Plants & Trees
Boating
Pollution - Air Quality Control
Crime Scene Investigation
Pools and Spas (Recreational)
Criminology
Postal Services
Digital Forensics
Power Supplies
DNA (Deoxyribonucleic Acid)
Product Liability
Education & Schools
Professional Skills
Elevators - Escalator - Automatic Doors
Psychology
Engineering
Real Estate
Expert Witnessing
Refrigeration - Cooling Systems
Feng Shui
Research Methodology
Finance
Scuba Diving
Hotels & Hospitality
Security
Human Factors
Sexual Abuse - Molestation - Harassment
Languages
Taxation
Life Expectancy - Life Care Planning
Telecommunication
Machinery
Terrorism - Homeland Security
Maintenance
Trial Presentations - Demonstrative Evidence
Medical Physics
Underwriting
Medicine
Waterproofing
More...
Failure Analysis Consultant Thomas Read
Thomas Read, PhD
Principal
1435 Fulton Rd.
Santa Rosa CA
95403
USA
phone: 707-544-2374
fax: 707-544-2370
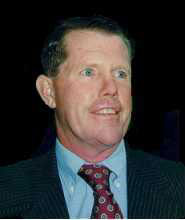
Expert Background: Dr. Thomas L. Read is the Principal and CEO at A. Read Consulting, LLC. He received his PhD. from Stanford University in 1972 and has over 25 years of manufacturing experience in electronics, metallurgy, factory safety, failure analysis, glass fracture, glass failure and bottle failure. As a member of the electronics industry, he has earned process patents and has an extensive background in manufacturing techniques.
In parallel, Dr. Read has spent over twenty five years as a consultant to attorneys and engineers. He has given more than 100 depositions and has appeared in court numerous times.
Company Profile: Read Consulting, LLC is a full service laboratory providing services in the following areas:Failure Analysis; Factory Safety and Personal Injury (including machine guards and manufacturing safety) Glass Failure Analysis - Glass Fracture, Glass Failures and Bottle Failure Metal and Ceramic Failure Grinding Wheel Failures Intellectual Property and Patent Disputes Product Liability and Product Quality Manufacturing Disagreements (such as Intellectual Property, Failed equipment and Contract Disputes) Reverse Engineering
In parallel, Dr. Read has spent over twenty five years as a consultant to attorneys and engineers. He has given more than 100 depositions and has appeared in court numerous times.
Company Profile: Read Consulting, LLC is a full service laboratory providing services in the following areas:
12/20/2023
· Failure Analysis
By: Dr. Thomas Read
California materials failure laboratory, Read Consulting Failure Analysis Laboratory was engaged to determine the cause of failure of a 12 oz soda bottle. This bottle was said to have exploded and caused injury to a person. The bottle was said to have spontaneously exploded as the was being pushed into a cooler filled with ice.
2/17/2023
· Failure Analysis
By: Dr. Thomas Read
When this type of valve is open a rubber seal around the valve stem prevents leaking. In this case, the poly acetate stem deteriorated due to the presence of hot chlorinated water This allowed water to leak out. Over time the leak rate increased.
10/24/2022
· Failure Analysis
By: Dr. Thomas Read
Read Consulting Failure Analysis Laboratory was engaged to determine the cause of failure of two titanium surgical screws used in corrective back surgery. These were both 6.5 mm diameter, 40mm long screws that were surgically implanted. in a patient, and they subsequently failed.
4/20/2022
· Failure Analysis
By: Dr. Thomas Read
The fatigue failure initiated on the outside bottom where the carafe had been scratched with the abrasive scrub pad. As a result of cyclical thermal shock (between 195°C and 15°C), the cracks grew progressively till it reached a critical length. Glass thickness at the origins is approximately 3 mm. One failed after 12.
4/12/2021
· Failure Analysis
By: Dr. Thomas Read
The annealed borosilicate glass pie plate failed as a result of “thermal shock”. There were multiple origins for the failure, and these all initiated at damage sites on the bottom of the Pyrex baking dish. It appears that the bottom of the pie plate was convex. Thus, setting the dish down and moving it on hard (abrasive) surfaces such as tile or granite counters created bottom “rim” damage.
9/6/2017
· Failure Analysis
By: Dr. Thomas Read
As "water hammer" (i.e. liquid impact) has the potential to cause glass bottle failure, Read Consulting LLC created two such failures to study the resulting fracture surface details.
4/23/2015
· Failure Analysis
By: Dr. Thomas Read
Read Consulting was asked to determine why a welded chair failed and caused injury to the person sitting in it.
2/3/2014
· Failure Analysis
By: Dr. Thomas Read
The root cause of the failure of customer returns of heated automobile rear view mirrors was investigated.
8/7/2012
· Failure Analysis
By: Dr. Thomas Read
During normal operation, the arm on an automatic wafer test station failed. Root cause failure analysis determined that the drive shaft on the right angle gear motor used to raise and lower the manipulator arm had failed first.
5/21/2012
· Failure Analysis
By: Dr. Thomas Read
This grinding wheel was part of a product liability and personnel injury case. It was claimed that the subject wheel had unexpectedly failed (i.e. flown apart) and an escaping piece had hit the plaintiff in the face causing serious injuries. According to the user, the grinder with the wheel was purchased approximately one hour before the grinding wheel failure.
3/29/2012
· Failure Analysis
By: Dr. Thomas Read
A failed plastic lawn chair was examined to determine the cause of failure. This chair failed on the premises of a restaurant In this study the subject chair is examined and compared to several exemplar purchased at the same time. The objective of this study is to determine the cause of failure.
11/8/2011
· Failure Analysis
By: Dr. Thomas Read
Glass Failure Analysis Expert Witness performs a failure analysis of a several tempered glass doors that had "spontaneously" failed at a construction site. The objective of this glass failure analysis is to determine the cause of failure and make recommendations to the contractor.
8/30/2011
· Failure Analysis
By: Dr. Thomas Read
Materials failure analysis expert performs a failure analysis to determine the source of a metal piece found in tomato product.
5/17/2011
· Failure Analysis
By: Dr. Thomas Read
A plumbing failure analysis was performed to determine why a cold water supply line to a bathroom sink had failed after only one year of service.
4/1/2011
· Failure Analysis
By: Dr. Thomas Read
A glass failure expert witness performs a root cause failure analysis on an exploding beer bottle. The object of this root cause failure analysis is to determine the cause of the bottle failure.
7/7/2009
· Design
By: Dr. Thomas Read
Before expending the effort necessary to reverse engineer a device or object, it must be definite that the object under study is not covered by one or more patents. This avoids a dispute over patent violations. Once it has been established that no patent coverage exists, one can use multiple techniques to reverse engineer a product. These are summarized below:
7/7/2009
· Failure Analysis
By: Dr. Thomas Read
The cracked tank was first inspected in the "as received" condition. In this condition it was cracked, but it was still whole. Next, the failed tank was separated by pulling it apart. This was done to expose the fracture surfaces of the main crack. This allowed for a complete failure analysis and for a determination of where the crack initiated.
7/7/2009
· Failure Analysis
By: Dr. Thomas Read
Glass fractography is the most effective method for determining why a glass object, such as a bottle, failed. This technique consists of examining the fracture surfaces of the failure for artifacts such as Wallner lines and using them to trace the crack back to its origin. Once the origin has been identified, it can be examined in detail with a microscope to determine the cause of the failure.
1/28/2006
· Failure Analysis
By: Dr. Thomas Read
Note: Glass Fractography is the most effective method for determining why a glass object, such as a bottle, failed. This technique consists of examining the fracture surfaces of the failure for artifacts such as Wallner lines and using them to trace the crack back to its origin
Related areas of expertise
Arbitration
Construction Accident Prevention& Safety
Construction Quality Control
Corrosion and Wear Failures Analysis
Electronic Engineering
Failure Analysis
Glass Engineering
Industrial Processes & Controls
Machinery Accident Prevention
Manufacturing Engineering
Materials Engineering
Mechanical Failure
Metals
Patent Infringement / Application
Polymers
Product Liability / Defects
Protective Coatings - Paint
Ceramic Tile - Stone - Wood
Construction Failure Analysis
Consumer Product Liability
Electrical Engineering
Engineering (General)
Glass / Windows / Windowall Construction
Glass Materials
International Arbitration
Manufacturing Accidents
Materials (General)
Materials Failure Analysis
Metallurgical / Metallurgy
Microwave Heating
Plastics Materials
Power Tools Safety
Product Safety
Workplace Safety
Featured resources
Law for the Expert Witness
by Daniel A. Bronstein
The Handbook of Healthcare Value: How...
by Bill Mohlenbrock MD
Essential Operational Components for...
by Jon Burroughs, MD, FACHE