Introduction
Read Consulting Failure Analysis Laboratory was asked to analyze a failed hot water shut off valve to determine the cause of failure. This was an under sink shut off valve in an upstairs bathroom.
When this type of valve is open a rubber seal around the valve stem prevents leaking. In this case, the poly acetate stem deteriorated due to the presence of hot chlorinated water This allowed water to leak out. Over time the leak rate increased.
Results Summary
The cut off valve has a design defect. Acetal plastic is not compatible with chlorinated water.
- The valve in question had leaked for some time.
- The degradation of the valve stem allowed water to escape past the rubber seal. Additionally, the seal deteriorated due to erosion from the escaping water.
- The acetyl plastic shaft degraded from hot chlorinated water and became brittle.
- The shaft broke in a brittle manner when an attempt to turn the valve off was made.
Procedure: Methods of Evaluation:
- Visually.
- Low Power Microscope.
- Fourier Transform Infrared (FTIR) analysis: This technique was used to identify the valve shaft polymer.
Results and Discussion
Visual and Low Power Microscope: Figure #1 is a photograph of the two pieces of the failed valve. In Figure #2 are close up photomicrographs of the fracture surfaces of the failed valve stem.
Fourier Transform Infra-red Analysis (FTIR): The FTIR analysis confirms that the valve post is made from Acetyl plastic (i.e. Delrin).
Discussion
The initial crack on the stem defeated the rubber seal and caused leaking. Basically, the acetal stem degraded due to the presence of hot chlorinated water. It is a known fact that Delrin is attacked by chlorinated water. The degradation will be higher if the chlorinated water is heated. Over time, erosion will increase the leak rate.
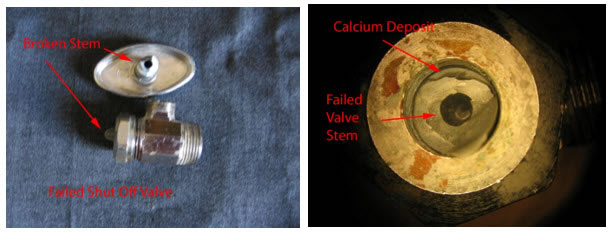
Figure #1: Photograph of the two pieces of the failed valve. Initially the stem cracked where the deposit exists and the valve leaked. The torsional overload occurred when an attempt was made to close the valve.
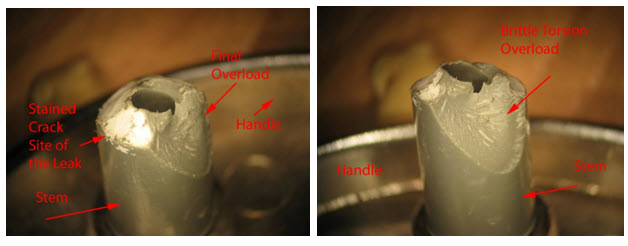
Figure #2: Close up p of the two fracture regions of the failed valve stem. Initially the stem cracked where the deposit exists, and the valve leaked. The torsional overload occurred when an attempt was made to close the valve.
Dr. Thomas L. Read, CEO of Read Consulting received his PhD. from Stanford University in 1972. He has over 25 years of manufacturing experience in electronics, metallurgy, factory safety, failure analysis, glass fracture, glass failure and bottle failure. As a member of the electronics industry, Dr. Read has earned process patents and has an extensive background in manufacturing techniques. In parallel, he has spent over twenty five years as a consultant to attorneys and engineers in the areas of failure analysis, metallurgy, glass fracture, glass failure, bottle failure, factory safety, manufacturing problems, intellectual property and patent disputes.
©Copyright - All Rights Reserved
DO NOT REPRODUCE WITHOUT WRITTEN PERMISSION BY AUTHOR.