Introduction
California materials failure laboratory, Read Consulting Failure Analysis Laboratory was engaged to determine the cause of failure of a 12 oz soda bottle. This bottle was said to have exploded and caused injury to a person. The bottle was said to have spontaneously exploded as the was being pushed into a cooler filled with ice.
Glass Failure Analysis Results
The cause of the failure of a bottle is determined by performing a root cause glass failure analysis. The standard procedure is to assemble the failed bottle, determine the general location of the failure origin, use markings on the glass fracture surfaces to locate the failure origin and microscopically examine the origin to determine the cause of failure.
Results Summary
The failure analysis below demonstrates that the bottle failed as a result of impact to the bottle’s neck/shoulder region. The impact caused damage to the outside surface of the bottle at the origin. Because the bottle was unopened, it was under pressure. The cracks then grew rapidly driven by the bottle’s gas pressure (approximately 40 psi). Essentially, the pressurized bottle exploded, and pieces of glass were ejected by the exploding bottle; these cut a bystander. This bottle did not fail at the bottom as a result of it being pushed into a cooler filled with ice. It failed because it had been hit in the neck/shoulder region by a hard object.
Lesson: Do not toast with an unopened soda bottle. Open it first to relieve the pressure.
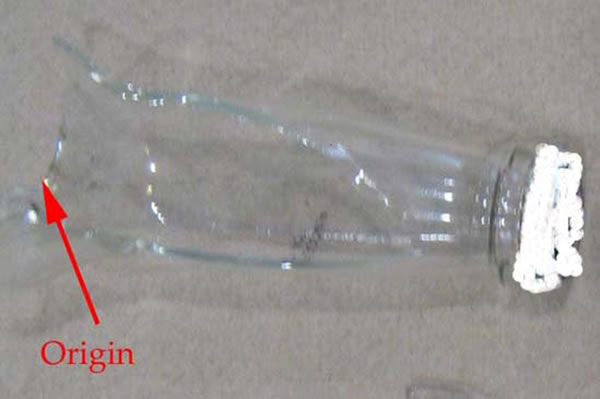
Figure #1: Neck portion of the broken bottle. Half of the origin is at the bottom of the neck. Note: the cap is still in place. Thus, the bottle was under pressure when it failed.
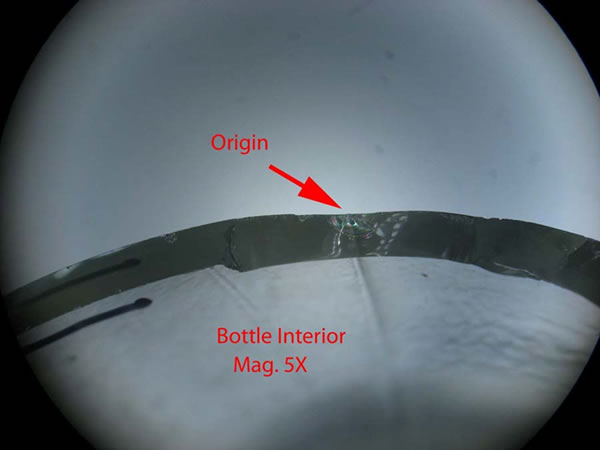
Figure #2: Neck portion of the broken bottle. Close up of Half of the origin at the bottom of the neck.
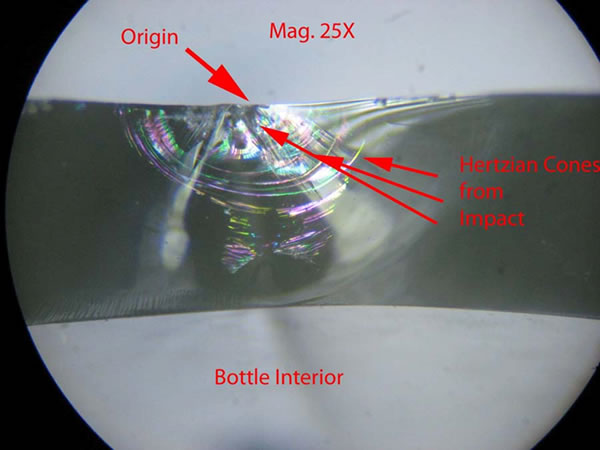
Figure #3: Photomicrograph of. Half of the origin at the bottom of the neck. The failure was caused by impact.
Dr. Thomas L. Read, CEO of Read Consulting received his PhD. from Stanford University in 1972. He has over 25 years of manufacturing experience in electronics, metallurgy, factory safety, failure analysis, glass fracture, glass failure and bottle failure. As a member of the electronics industry, Dr. Read has earned process patents and has an extensive background in manufacturing techniques. In parallel, he has spent over twenty five years as a consultant to attorneys and engineers in the areas of failure analysis, metallurgy, glass fracture, glass failure, bottle failure, factory safety, manufacturing problems, intellectual property and patent disputes.
©Copyright - All Rights Reserved
DO NOT REPRODUCE WITHOUT WRITTEN PERMISSION BY AUTHOR.