Read Consulting Failure Analysis Laboratory was engaged to determine the cause of failure of two titanium surgical screws used in corrective back surgery. These were both 6.5 mm diameter, 40mm long screws that were surgically implanted. in a patient, and they subsequently failed.
Result Summary
Both screws were made from titanium, aluminum, vanadium alloy. In addition, both failures are attributed to bending fatigue that initiated at the screw’s minor diameter (i.e. at the thread root). One failure initiated at what appears to be a “machining” or “turning” mark on the minor diameter. The other failure initiated at a very similar location, but there is no visible machining mark. In either case, the fatigue cracks started at a stress riser.
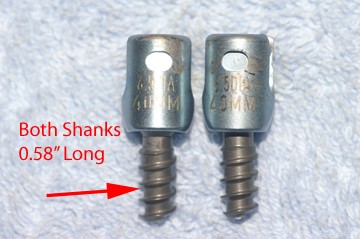
Figure #1: Photograph of the two failed screws.
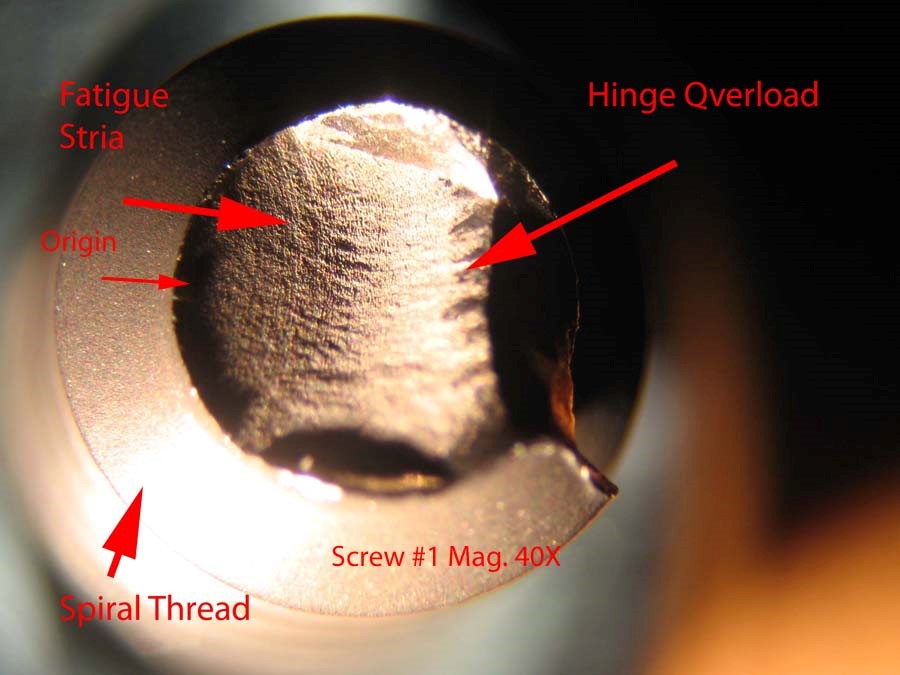
Figure #2: Photomicrograph of the fracture surface on screw #1. This fatigue crack appears to have started at the �root� of the thread.
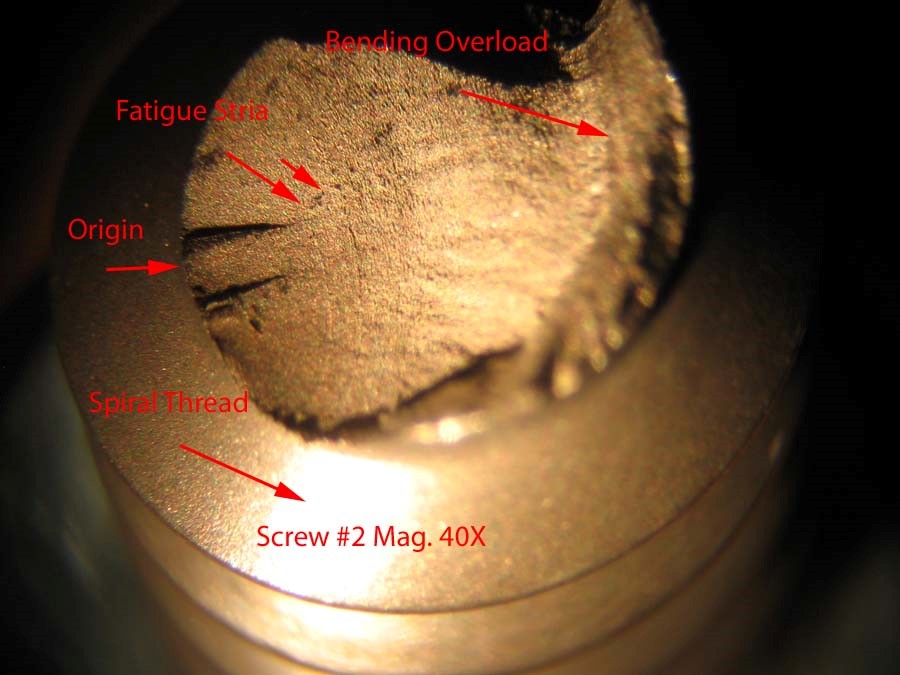
Figure #3: Photomicrograph of the fracture surface on screw #2. This fatigue crack appears to have started at a machining mark in the root of the thread.
Figure #2: Photomicrograph of the fracture surface on screw #1. This fatigue crack appears to have started at the �root� of the thread.
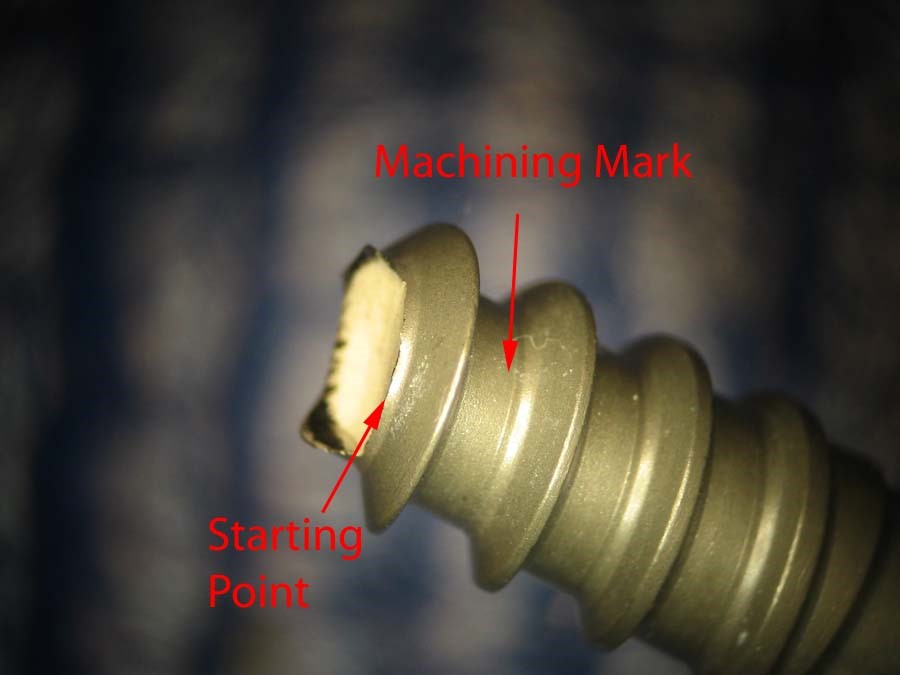
Figure #4: Photomicrograph side view of screw #2. This fatigue crack appears to have started at a machining mark in the "root" of the thread.
Dr. Thomas L. Read, CEO of Read Consulting received his PhD. from Stanford University in 1972. He has over 25 years of manufacturing experience in electronics, metallurgy, factory safety, failure analysis, glass fracture, glass failure and bottle failure. As a member of the electronics industry, Dr. Read has earned process patents and has an extensive background in manufacturing techniques. In parallel, he has spent over twenty five years as a consultant to attorneys and engineers in the areas of failure analysis, metallurgy, glass fracture, glass failure, bottle failure, factory safety, manufacturing problems, intellectual property and patent disputes.
©Copyright - All Rights Reserved
DO NOT REPRODUCE WITHOUT WRITTEN PERMISSION BY AUTHOR.